OCCUPATIONAL HEALTH & SAFETY RESOURCES
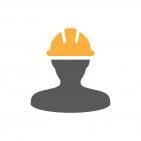
Maryland Occupational Safety and Health (MOSH) - https://www.dllr.state.md.us/labor/mosh/
Delaware Occupational Safety and Health – https://dia.delawareworks.com/osha-consultation/
Federal Occupational Safety & Health Administration (OSHA)
- Logging eTool - https://www.osha.gov/SLTC/etools/logging/index.html
- Logging OSHA Page - https://www.osha.gov/SLTC/logging/index.html
For a quick reference on some of the OSHA Logging Rules visit our summary page by clicking here
Additional OSHA Information
OSHA Logging Rules
OSHA Logging Rules
A partial list of Occupational Safety and Health Administration (OSHA) regulations, expressed in common working language, that apply to logging follows:
A. PERSONAL PROTECTIVE EQUIPMENT
1. Gloves shall be provided when working with wire rope.
2. The employer shall assure that each employee wear foot protection, such as heavy-duty logging boots, that cover and provide support to the ankle. Chain saw operators shall wear foot protection that is constructed with cut-resistant material that will protect against contact with a running chain saw.
3. Safety helmets shall be provided.
4. Eye or face protection shall be provided for use where chips and sawdust or flying particles are present.
5. Protection against the effects of noise exposure shall be provided when the sound levels are high enough to induce potential hearing loss.
6. First aid kits sufficient for the number of employees shall be provided at the work site and on all transport vehicles. First aid kits shall be regularly inspected and replenished.
B. WORK AREA SAFETY:
7. All work shall terminate and employees moved to a place of safety during electrical storms and periods of high winds or when other unusual weather conditions are dangerous to personnel.
8. Dead, broken, or rotted limbs or trees that are a hazard (widow makers) shall be felled or otherwise removed before commencing logging operations and before building roads, trails, or landings in their vicinity.
9. Each employee performing a logging operation at a logging work site shall work in a position or location that is within visual or audible contact with another employee.
10. An approved fire extinguisher shall be provided on each machine and on each vehicle.
C. CHAIN SAW SAFETY
11. Chain saw operators shall be instructed to inspect the saws daily to assure that all handles and guards are in place and tight, that all controls function properly, and that the muffler is operative.
12. Chain saw operators shall fuel the saw only in safe areas and not under conditions conductive to fire such as near men smoking, hot engine, etc.
13. Chain saw operators shall start the saw with both hands during operation.
14. Chain saw operators shall start the saw at least ten feet away from fueling area.
15. Chain saw operators shall start the saw only on the ground or when otherwise firmly supported.
16. Chain saw operators shall be certain of footing and clear away brush which might interfere before starting to cut.
17. Chain saw operators shall shut off the engine or engage the chain brake when carrying it for a distance greater that 50 feet or in hazardous conditions such as slippery surfaces or heavy underbrush.
18. Chain saw operators shall not use the saw to cut directly overhead or at a distance that would require the operator to relinquish a safe grip on the saw.
D. EQUIPMENT OPERATIONS SAFETY
19. Equipment operators shall be instructed as to the manufacturer's recommendations for equipment operation, maintenance, safe practices, and site operating procedures.
20. Equipment shall be kept free of flammable material.
21. Equipment shall be kept free of any material which might contribute to slipping and falling.
22. Engine of equipment shall be shut down during fueling, servicing, and repairs except where operation is required for adjustment.
23. Equipment shall be inspected before each workshift begins. Defects or damage shall be repaired or replaced before work is commenced.
24. The equipment operator shall walk completely around machine and assure that no obstacles or personnel are in the area before startup.
25. The equipment operator shall start and operate equipment only from the operator's station or from a safe area recommended by the manufacturer.
26. Seat belt shall be provided on mobile equipment.
27. The equipment operator shall check all controls for proper functions and response before starting working cycle.
28. The equipment operator shall maintain adequate distance from other equipment and personnel.
29. The equipment operator shall not operate movable elements (boom, grapple, load, etc.) close to or over personnel.
30. The equipment operator shall dismount and stand clear for all loading and unloading of his mobile vehicle by other mobile equipment. The dismounted operator shall be visible to loader operator.
31. The equipment operator shall not permit riders or observers on the machine unless approved seating and protection is provided.
32. The equipment operator shall shut down the engine when the equipment is stopped and apply brake locks and ground moving elements before dismounting.
33. When any equipment is being moved or operated in the vicinity of an electric distribution line, a minimum clearance of ten feet shall be maintained between the electric distribution line and all elements of the machine.
34. A protective canopy shall be provided for the operator of mobile equipment. It shall be so constructed as to protect the operator from injury due to falling trees or limbs, saplings, or branches which might enter the compartment side areas, and snapping winch lines or other objects.
E. TREE FALLING SAFETY
35. Work areas shall be assigned such that a tree cannot fall into an adjacent work area. The recommended distance between workers is twice the height of the trees being felled.
36. Workers shall not approach a feller closer than twice the height of trees being felled until the feller has acknowledged the signal of approach.
37. Each danger tree shall be felled, removed or avoided. Each danger tree, including lodged trees and snags, shall be felled or removed using mechanical or other techniques that minimize employee exposure before work is commenced in the area of the danger tree.
38. If the danger tree is not felled or removed, it shall be marked and no work shall be conducted within two tree-lengths of the danger tree unless the employer demonstrates that a shorter distance will not create a hazard for an employee.
39. The feller shall plan a retreat path and clear path as necessary before cut is started.
40. The feller shall appraise suituation for dead limbs, the lean of tree to be cut, wind conditions, location of other trees and other hazards, and exercise proper precautions before cut is started.
41. Undercuts shall be of a size so the tree will not split and will fall in the intended direction.
42. A backcut shall be made in each tree being felled. The backcut shall leave sufficient hinge wood to hold the tree to the stump during most of its fall so that the hinge is able to guide the tree's fall in the intended direction.
43. The saw shall be shut off or the throttle released before feller starts his retreat.
44. On terrain where trees are likely to slide or roll, fellers shall fell trees from the uphill side and arrange to keep uphill from previously felled trees.
45. Bucking and limbing on any slope where rolling or sliding of trees or logs is reasonably foreseeable shall be done on the uphill side of each tree or log.
46. When a spring pole or other tree under stress is cut, no employee other than the feller shall be closer than two tree lengths when the stress is released.
F. SKIDDING SAFETY
47. Only a designated, trained operator shall operate a skid or prehaul machine.
48. Choker setters shall work on uphill side of log.
49. No passenger personnel shall ride on a prehaul vehicle, logs, pallets, skid pans, or other load unless adequate seating and protection is provided.
50. During winching, the equipment shall be positioned so that the winch line is in alignment with the long axis of the prehaul machine.
51. Each log shall be placed on a transport vehicle in an orderly manner and tightly secured. The load shall be positioned to prevent slippage or loss during handling and transport.
52. The transport vehicle operator shall assure that each tie down is tight before transporting the load. While enroute, the operator shall check and tighten the tie downs whenever there is reason to believe that the tie downs have loosened or the load has shifted.
FOR MORE OSHA INFORMATION:
This is not intended to be a complete listing of the OSHA regulations. For a more comprehensive treatment of OSHA Rules, see the Forest Resource Association publication 95-A-14: The Loggers Guide to the New OSHA Logging Safety Standards. OR check their website: loggingsafety.com
or contact the Forest Resource Association:
Mr. Rick Meyer, Division Forester
Appalachian Technical Division
Forest Resources Association
2129 Electric Road, SW, Ste 205
Roanoke, VA 24018
Phone: 540-989-4171
Fax: 540-774-9415
E-Mail: meyerforest@aol.com website: www.forestresources.org
or Contact OSHA:
US Department of Labor
Occupational Safety & Health Administration
200 Constitution Avenue, NW
Room Number N3626
Washington, D.C. 20210
800-321-6742 (OSHA)
or visit the OSHA Logging Safety website.
MARYLAND LOGGING REGULATIONS
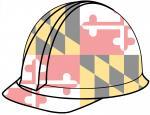
In order to legally log in the State of Maryland you must obtain a Forest Product Operator’s License (FPO) from the MD Department of Natural Resources (DNR). You are also required to obtain the Forest Harvest Green Card from the Maryland Department of the Environment (MDE) in order to file a Sediment Control Plan
FPO License application can be found at: http://dnr.maryland.gov/forests/Documents/fpoapp.pdf
- Renewal is required ANNUALLY and done by filling out the form, selecting “Renewal” and submitting it with payment
- For more information about the Forest Product Operator's License, visit: http://dnr.maryland.gov/forests/Pages/fpo_search.aspx
Forest Harvest Green Card information
-
Sustainable Forestry I: Sediment and Erosion Control, Spill Cleanup and Prevention, Logging Aesthetics is the training course provided by the University of Maryland Extension Master Logger Program that must be taken in order to receive the Forest Harvest Green Card. For information on how to register for this training please visit our Master Logger Training page
OR
- visit the MDE’s Sediment and Erosion Control website for more information on MDE’s role in protecting Maryland’s environment: https://mde.maryland.gov/programs/Water/StormwaterManagementProgram/Pages/erosionsedimentcontrol.aspx
Sediment & Erosion Control Plan information
Please Note: Any Forest Harvest Operation that disturbs more than 5,000 square feet or 100 cubic yards of soil must have an approved Sediment and Erosion Control Plan - See S&E Control Manual for Forest Harvest Operations
- A Standard Erosion and Sediment Control Plan for Forest Harvest Operations in Maryland (Standard Plan) has been developed by the MDE and DNR to help assist loggers with meeting this requirement. The Standard Plan covers most basic harvest sites, includes general erosion and sediment control requirements for a harvest operation, and may be obtained at any Soil Conservation District office.
- Ensure that you have an understanding of all permit and inspection requirements for each county as they vary depending on site location
- S&E Plans are done through Soil Conservation Districts, of which a list can be found here: https://mda.maryland.gov/resource_conservation/Pages/technical_assistance.aspx
NEW! Maryland Forest Service Site Reviews
The Maryland Department of Natural Resources Forest Service will conduct forest harvest site visits on active logging operations across the state, in a joint effort with the Maryland Department of the Environment to protect natural resources, wetlands, and waterways during forest harvest operations.
For more information on Maryland's Forest Service Site Reviews visit: https://go.umd.edu/FSsitevisits
DELAWARE LOGGING REGULATIONS
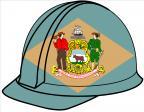
- There is no Green Card equivalent for the State of Delaware
- Anyone is able to obtain a permit as a forest operator
You will be required to obtain a Road Entrance Permit from DelDOT
- The application can be found online at https://services.deldot.gov/EPSExternal/EPSpermit
- For DelOT Entrance Permit FAQ’s visit: https://www.deldot.gov/business/entrance-permit-system/faqs/
- All information regarding Delaware timber harvests, rules and regulations, and BMPs can be found at: https://agriculture.delaware.gov/forest-service/
For more information regarding Delaware’s Regulations and Permits, visit: https://agriculture.delaware.gov/forest-service/landowner-assistance/
MARYLAND WOODLAND OWNERS
Call Before You Cut ProgramThe program provides Maryland woodland owners with free information to ensure that they harvest their timber in the most efficient, cost-effective, and ecologically-sound manner possible. The Maryland Call Before You Cut program offers online information at: www.callb4ucut.com/maryland |